在现代电动汽车电池组中,为了最大限度地提高能量密度,电池单元被紧密排列,单元之间的间距通常小于1毫米。在正常运行期间,这些电池单元的电压差可能超过400V,而热事件可能导致温度超过150°C——在这种情况下,即使是轻微的绝缘故障也可能导致灾难性的短路。
根本的挑战在于保持电池之间可靠的电隔离,同时尽量减少绝缘材料专用的空间并保持热管理能力。本文汇集了7大应用解决方案,包括防止分层和烧穿的复合外壳材料、兼具机械和电气保护的组件隔热材、具有各向异性或定向传热等。这些方法及其他方法均侧重于在量产车辆中平衡安全要求与能量密度目标的实际应用。
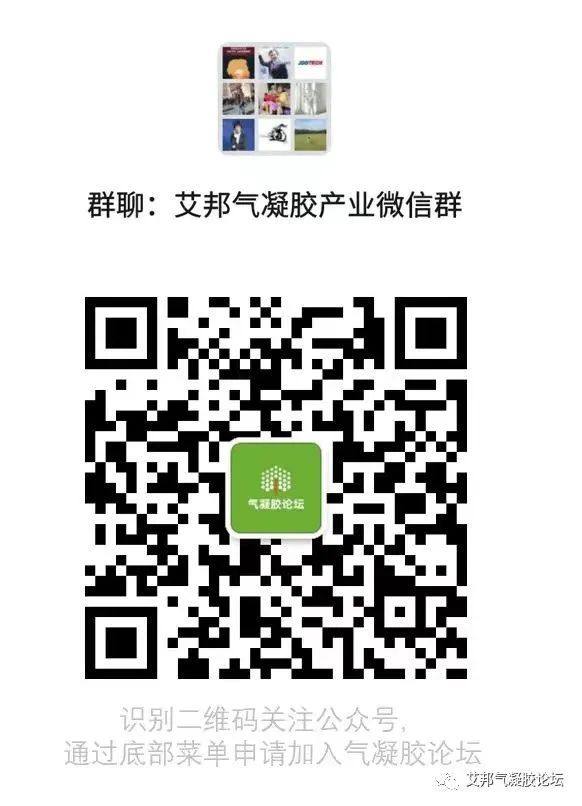
1. 用于防止热失控的气凝胶多层隔热板和复合屏障
电动汽车 (EV) 电池系统的热失控是制造商和设计人员面临的最重大安全挑战之一。硅胶泡沫和云母板等传统绝缘材料虽然能够满足基本需求,但在机械韧性、成本效益以及极端条件下的结构完整性方面却存在严重缺陷。
解决这些局限性的一项重大进展是采用夹层结构的多层气凝胶复合隔热板。这些隔热板的特点是将气凝胶芯封装在两层保护层之间,从而显著增强了抗压和抗弯性能,同时保持了优异的隔热性能。这种封装设计具有双重目的:防止易碎的气凝胶芯产生粉尘,并减缓材料老化,从而为电动汽车电池组提供更耐用、更易于集成的解决方案。这种方法在多层气凝胶复合隔热板设计中得到了详细阐述,与传统的易碎隔热材料相比,它代表了显著的改进。
对于需要极端温度适应性的应用,复合壳体结构将陶瓷浆料基隔热层与二氧化硅气凝胶隔热层相结合。隔热层采用陶瓷浆料和碳化硅纤维布的双重结构,具有卓越的耐烧蚀性能。隔热层由纳米二氧化硅气凝胶复合毡构成,具有卓越的隔热性能。这种一体化设计可承受1300°C火焰直接照射30分钟,而不会出现分层或结构破坏。值得注意的是,其烧蚀后抗弯强度保持在100MPa以上,远远优于云母或陶瓷纤维板等传统材料。
为应对隔热和横向散热的双重挑战,气凝胶阻燃片材集成了两层气凝胶基隔热层,并巧妙地布置了铜箔或石墨烯导热层。导热元件的几何排列有利于向下流动,有效防止垂直热扩散,同时保持横向电池隔离。这种结构兼具防火性、定向热管理和机械柔韧性,且结构轻巧紧凑,适用于高密度电动汽车电池系统。
2. 用于防止分层和烧穿的气凝胶+预氧化碳化硅毡隔热层
随着电动汽车制造商不断追求更高的能量密度,有效的热管理变得越来越重要。相变材料 (PCM) 代表了一种先进的被动热管理方法,其优势超越了传统的隔热材料。
层压陶瓷复合材料外壳通过由碳化硅纤维增强陶瓷浆料制成的耐热层,以及由纳米二氧化硅气凝胶和预氧化碳化硅毡组成的隔热层,解决了这些局限性。这种双层系统即使在1300°C的火焰烧蚀下长达30分钟也能保持结构完整性和隔热性,并将材料降解降至最低。
复合材料外壳的主要优势在于其轻质、可扩展且兼具耐高温和机械强度。优化的陶瓷浆料成分形成交联网络,可增强抗弯强度,同时防止分层和烧穿。纳米气凝胶材料进一步降低了热导率,最大限度地减少了向内部电池模块的热量传递。该结构还支持在热事故期间安全泄压,从而降低连锁故障风险,同时保持与现有制造技术的兼容性。
3. 用于电池组外壳的气凝胶+双层陶瓷化浆料体系
高容量锂离子电池的热失控和短路传播风险推动了能够在极端条件下保持热完整性和机械完整性的先进绝缘材料的开发。
对于需要兼顾热防护和结构强度的电池组外壳,多层复合材料外壳结构可提供全面的保护。该设计采用由硅树脂和陶瓷颗粒组成的双层陶瓷浆料体系,涂覆在碳化硅纤维布上,形成隔热层。纳米二氧化硅气凝胶复合材料制成的隔热组件位于该保护层下方。这些组件共同构成一道屏障,能够承受高达 1300°C 的火焰直接照射 30 分钟,且材料损失和结构性能均保持在最低水平。
复合材料外壳集成了耐烧蚀和机械增强功能,使电池组即使在极端高温条件下也能保持抗弯强度。传统材料在这种应力下会降解或失效,而该解决方案则能保持烧蚀后机械强度超过100 MPa。优化的浆料配方减少了对昂贵的碳化硅纤维的依赖,并通过溶剂稳定分散提高了工艺效率,从而能够制造出轻薄、高性能的电池外壳。
4. 用于机械和电气隔离的气凝胶复合材料
电池组中的隔热材料必须能够承受极端温度变化,同时保持结构完整性。一般而言,由电池组间的垫片和垫圈发挥作用,它们既能提供机械稳定性,又能提供电气隔离。传统的垫片在发生物理损坏时通常无法提供即时绝缘,从而容易发生短路。二氧化硅气凝胶陶瓷纤维复合材料解决了传统材料易受烧蚀、起火或结构不均匀等缺陷的难题。
该复合材料将陶瓷纤维布基与二氧化硅气凝胶基质相结合,并使用阻燃薄膜或涂层进行封装。严格的尺寸公差和均匀的密度消除了吸热空隙,而气凝胶的超低导热性则确保了电池之间的热传递最小化。该结构可防止热扩散,同时在热应力下保持完整性。
5. 用于电池芯顶部和侧面的气凝胶隔热层/板
在热管理方面,隔热铝板结构通过填充二氧化硅气凝胶粉末的蜂窝层(由铝板包裹)延缓了热失控在电池模块间的传播。二氧化硅气凝胶的低导热性与蜂窝状几何形状相结合,可有效抑制电池单元之间的热传递,从而提供关键的排气时间,并最大限度地降低全模块起火的可能性。该设计支持制造可扩展性,并提供单面板配置等选项,从而减少材料使用并简化生产。
在单个电池层面,应用于电池芯顶部和侧面的隔热层采用导热系数低于 0.2 W/m·K 的材料,以针对最易受热和火焰穿透的区域。通过阻止热失控电池的热量流动,该隔热层可限制热传播至相邻电池的风险,而不会显著影响能量密度或机械结构。
6. 电池模块或电池组间的气凝胶基绝缘隔热系统
7. 各向异性或定向传热的气凝胶隔热材料
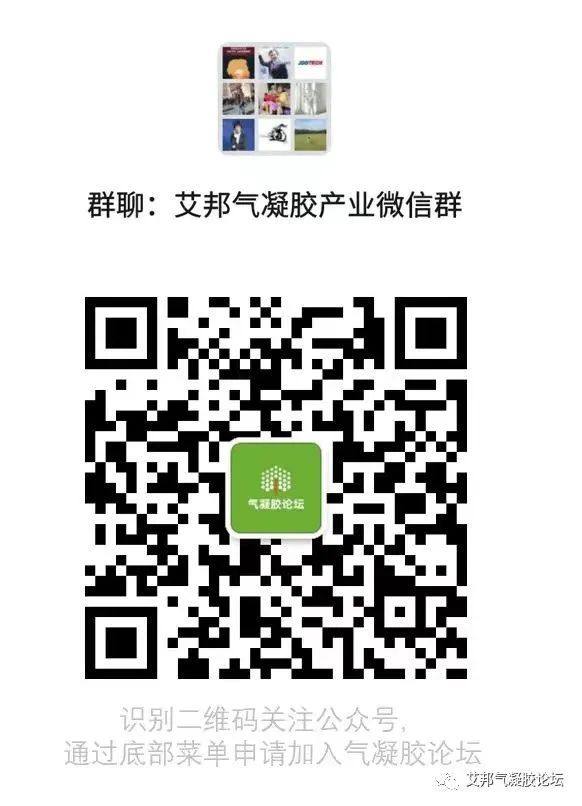
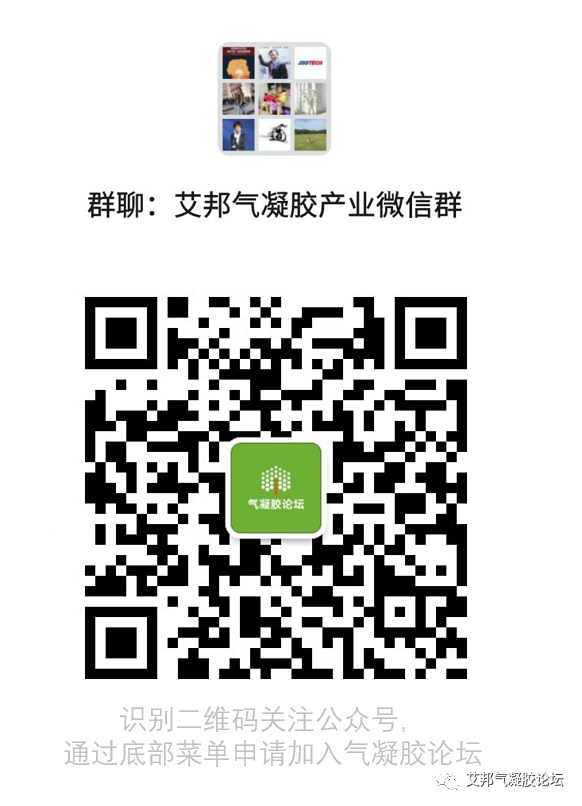