由于纳米气凝胶隔热毡/片的生产工艺采用液压模压成型,可根据需要采用不同的模具生产不同形状的纳米气凝胶隔热毡,同时,根据不同温度需要,生产不同温度使用的隔热材料。


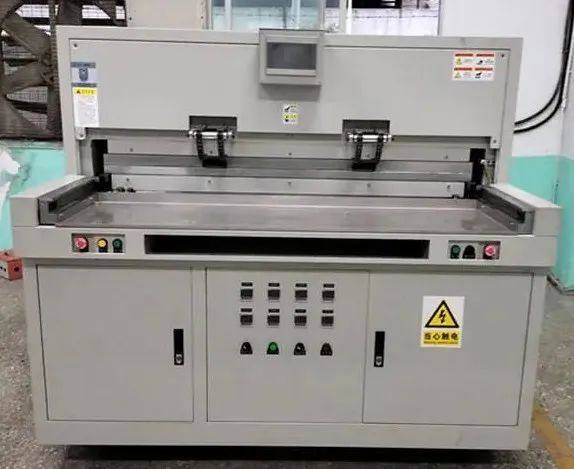
① 打开机台电源→根据不同的制品设置相应的参数待机启动,让机台升温到指定的温度。
② 待机复位→手动放板→型入→抽真空→油缸上升→预压计时→油缸加压→成型计时→气囊增压→成型结束→释放真空→油缸下降(自动)→型出→手动拿料。
完成一个工作流程,按此步骤循环压合即可。


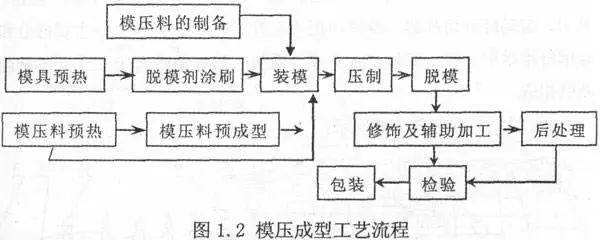
在液压模压成型中要注意控制模压温度、模压压力及模压时间等三个工艺参数。
压缩成型所规定的横温就是模压温度。物料在接触横壁处升温快,先交联反应形成硬壳,内部稍后交联、固化、收缩,因受硬外壳限制而承受拉应力。固化后的塑件表层有残余压应力,内部有残余拉应力,这些残余应力的存在是塑件成型后出现翘曲、开裂、强度下降的原因。
每一种热固性塑料有其合适的模压温度范围。模压温度过高,交联反应快;成型形状复杂、薄壁、深腔塑件时,常因物料流动性下降而难以充满模腔。过早形成的硬壳,阻碍内部交联而产生的低分子挥发物向外排出,导致塑件脱模后出现肿胀、翘曲、开裂。
② 模压压力
压缩成型时在施压方向上模腔单位投影面积上所受到的压力。它的作用是使塑料增密、促进物料流动、平衡模腔内低分子挥发物所产生的压力。高模压压力使塑件密度增大,成型收缩量减小,增大物料流动,克服肿胀,防止出现气孔。
但也会增大塑件内部残余应力。应根据材料性能、配合模温,选定合适的模压压力。表观密度低、散状料、乱纤维状塑料等需用高模压;模塑预压物、粉状料可用低模压。
③ 模压时间
成型时间(成型周期)成型时间是加料、合模、排气、加压、固化、脱模、模具清理、安放嵌件或组合模瓣等工序所需的时间的总和。即模具完全闭合后或最后一次卸压排气闭模后到开启模具之间,物料在模内受热固化的时间。
它的作用是使压制品充分交联、固化定型,达到预期的物理机械性能或特定的使用性能指标。模压时间与塑料类型和组成、塑件的形状和壁厚、模具结构、模压温度及模压压力、预压、预热及卸压排气等多种因素有关。
来源:鑫台铭、欧能机械
原文始发于微信公众号(艾邦气凝胶论坛):气凝胶隔热片液压成型工艺与主要控制因素
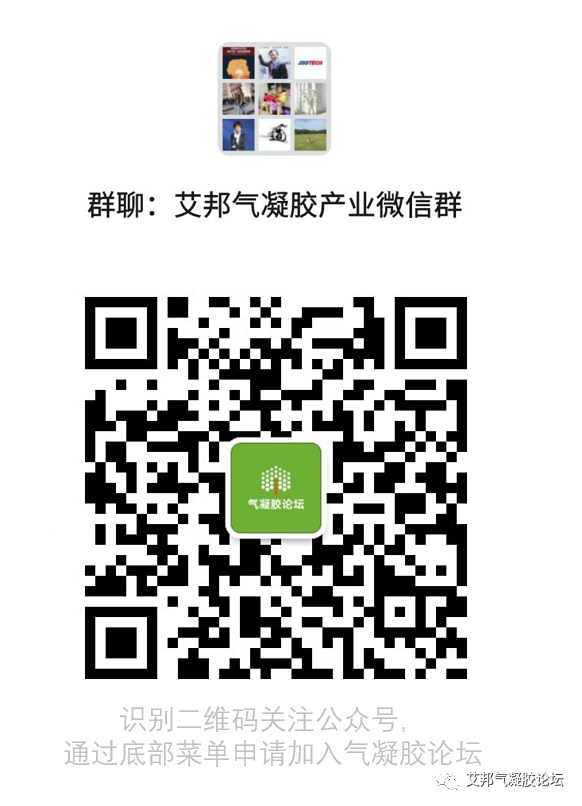